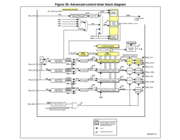
Low-level STM32 Peripheral access
While Espruino provides an easy-to use way to access the peripherals on the microcontroller, the hardware itself is amazingly complex and capable, and can do far more than can be exposed to you in JavaScript.
If you want to really make the most of the hardware, you'll have to access it directly. Here, we'll detail how to access the timer hardware to measure pulse length on the STM32 microcontrollers used in the Original Espruino and the Espruino Pico.
Documentation
The best source of documentation on the chip's peripherals come from the manufacturer themselves - ST. You'll need the Reference Manual and Datasheet for the particular chip. The easiest way to do this is to go to the page on espruino.com for your board (Original or Pico and to find the links there).
We're going to cover the Pico, so this is the STM32F401CD Reference Manual and this is the STM32F401CD Datasheet.
It's a huge manual, but you're only interested in specific parts of it.
What happens for PWM
First off, look at Advanced-control timer (TIM1)
on page 241. We're going to look at what happens when you
write analogWrite(A8, 0.5, {freq:10})
.
You'll see a diagram of the timer a few pages in:
Here, we've coloured what bits get used during analogWrite(A8, 0.5, {freq:10})
.
First, Espruino looks around to see what peripherals are available on the pin A8
. That information
is in the Datasheet, under Pinouts and pin description
in a table called Table 8. STM32F401xD/xE pin definitions
(look for PA8
in it).
It's actually pretty painful to read, so we've documented it all properly on the Pico page.
Under the Pinout
heading hover your mouse over the PWM
tag below the pin A8
. It'll say TIM1_CH1
-
so Channel 1 of the TIM1
peripheral.
Now, Espruino will make sure the STM32 applies power to TIM1
(it'll be off by default to save power).
Then, Espruino configures the pin itself:
- On STM32F4 chips (like in the Pico), each pin has a 4 bit
register associated with it called the 'Alternate Function' register. Internally, the pin can be
'wired' to different peripherals (in this case I2C3, TIM1, and USART1) and the number you write
into that register determines what it's connected to. If you look at
Table 9. Alternate function mapping
in the datasheet you'll see that to getTIM1_CH1
inPA8
you needAF01
- so Espruino writes1
into that register. - STM32F1 chips (like in the Original Espruino) are a bit older, and as such have a slightly
more painful way of handling alternate functions. Each peripheral has an alternate function
register, so for instance if you wanted to put
TIM1_CH1N
onto pinA7
on an STM32F1, you'd setTIM1
's alternate function to 1 - but then it'd moveTIM1_CH1
to pinE9
, along with everything else!
Now Espruino's done all that painful stuff, it'll configure the timer itself. It:
- Sets up the prescaler to divide the Pico's 84Mhz clock down, such that the 16 bit
counter
CNT
counts up from 0 to 65535 just less than 10 times per second (because we set the frequency to s0). - Sets the
AutoReload Register
(ARR
) to fine-tune the frequency, by only letting the counter count up to a value a bit less than the full 16 bit value 65535 (just setting the prescaler wouldn't have been accurate enough!) - Sets
Capture/Compare register 1
(CCR1
) to theAutoReload Register
multiplied by the duty cycle (in this case it's0.5
) - Sets up the
Output control
register so thatTIM1_CH1
is high wheneverCNT
is less than theCapture/Compare register
's value - Enable the timer itself by writing to the enable bit.
Finally it's done, and the A8
will be outputting a square wave at 10Hz.
Accessing the Timer
So, that was all pretty heavy. While the Reference manual does walk you through what's needed, that's a lot to learn for a PWM output.
All of those things that Espruino did were done by modifying the peripheral registers - bits of memory at certain locations that control how the peripherals work.
If you go to the end of the chapter in the reference manual, you'll find 12.4 TIM1 registers
. These are descriptions of exactly which bits of the registers do what.
So let's access CCR1
(Capture/Compare register 1) - the register that Espruino put the duty cycle in, and see what it is. If you look it up,
at 12.4.14 TIM1 capture/compare register 1 (TIMx_CCR1)
you'll see it says Address offset: 0x34
- this is the address offset in TIM1
.
So now, you want to find the address of TIM1
itself. Go to 2.3 Memory map
in the reference and look at the table. The entry for TIM1
says: 0x40010000 - 0x400103FF - TIM1
.
Ok, so we're getting somewhere - the address of CCR1
is 0x40010000 + 0x34
- so 0x40010034
. Let's look in there at what's in the register - it's a 16 bit value, so we'll use peek16
.
First, type var CCR1 = 0x40010034;
to store the address. Then type peek16(CCR1)
and you should get 0
- because we haven't run analogWrite
yet.
Get some breadboard, and connect up an LED to pin A8
, with a 100 Ohm (or close) resistor:
Then run analogWrite(A8, 0.5, {freq:10})
- the LED should now be blinking 10 times a second, all done by hardware.
Try peek16(CCR1)
again to get the value of CCR1
- it's now saying 32307
.
Try setting the LED to blink only very quickly with analogWrite(A8, 0.05, {freq:10})
and then check peek16(CCR1)
. You'll see that as you'd expect, the value is now one tenth of what is was. It's 3230
.
By itself that's not useful, but we can actually change it ourself, using poke
.
- Try
poke16(CCR1, 0)
- this should set the duty cycle to 0, turning it off. - Or try
poke16(CCR1, 40000)
to make it stay on most of the time.
We can guess at how far the counter CNT
is counting, because we knew that a duty
cycle of 50% meant 32307
in CCR1
(it'll be around 2 * 32307
). However, to check,
we can look in ARR
(AutoReload Register
). The Reference Manual say's it's at offset 0x2C
,
so let's try var ARR = 0x4001002C;
and then peek16(ARR)
. It returns 64615
which is again what we'd expect.
But we can change that. If we make it lower, the timer will count down from a lower value so the LED will blink faster.
Try poke16(ARR, 30000)
and the timer should now count twice as fast. The LED will now be on constantly though, because the counter is counting between 30000 and 0, but we set CCR1
to 40000. Set it to something lower, with poke16(CCR1, 1000)
and the LED will now be flickering. If you experiment with poking different values into ARR
you'll get different speeds.
Finally, let's actually look at the value in the counter. It'll be moving quite quickly, so let's call analogWrite
again to slow it down: analogWrite(A8, 0, {freq:0.1})
The counter will now be counting up over a period of 10 seconds. In the reference manual, TIM1's counter CNT
is at offset 0x24
, so let's access that:
var CNT = 0x40010024;
peek16(CNT);
and now, keep hitting up arrow
followed by enter
, you should see something like:
>peek16(CNT);
=31807
>peek16(CNT);
=33273
>peek16(CNT);
=34583
>peek16(CNT);
=35900
>peek16(CNT);
=37161
>peek16(CNT);
=38458
>peek16(CNT);
=39767
>peek16(CNT);
So the counter is actually counting up.
Counting edges
So that was interesting, but not really useful. What if we wanted to actually count the amount of times a pin changed state?
Looking at the diagram again, we could use different parts of TIM1
:
So assuming Espruino has already set the timer up for our analogWrite
, what do we have to change?
- Set
A8
to the correct state - Enable the edge detector
- Make sure the 3 multiplexers are forwarding the signal from A8 to the right place
- Reset the prescaler so it doesn't prescale at all
- Reset the
Autoreload Register
(ARR
) to 0 so we can count all the way up to 65535
Ok, so let's jump in. First, connect pin A8
to pin A5
that's opposite on the Pico. We'll send some pulses from there later in order to test our timer.
Then, let's gets some registers defined - copied from the Reference manual again:
// slave mode control register
var SMCR = 0x40010008;
// event generation register
var EGR = 0x40010014;
// Capture compare mode register
var CCMR1 = 0x40010018;
// Capture/compare enable register
var CCER = 0x40010020;
// counter
var CNT = 0x40010024;
// prescaler
var PSC = 0x40010028;
// auto reload register
var ARR = 0x4001002C;
Now, let's go through in sequence:
Set A8
to the correct state
It turns out that A8
is already in the correct state - it was set as 'alternate function' and connected to TIM1 by analogWrite
, and that's enough.
Enable the edge detector
Take a look at 12.3.4 Clock selection
and under it, Internal clock source (CK_INT)
in the reference manual.
That's showing TI2
as an input, but TI1
is basically the same - we just change 2
for 1
in the instructions.
So we need to:
Configure channel 1 to detect edges on the
TI1
input by writingCC1S = ‘01’
in theCCMR1
register.Configure the input filter duration by writing the IC1F[3:0] bits in the
CCMR1
register - we don't need a filter so writeIC1F = 0000
Taking a quick look at the register definitions at the end of the chapter, CC1S
is the bottom 2 bits of CCMR1
, and IC1F
is bits 7 to 4.
However: in small text at the bottom of that it also says:
CC1S bits are writable only when the channel is OFF (CC1E = ‘0’ in TIMx_CCER).
As the channel is definitely on already (because we're using it for PWM) we've got to turn it off. Looking at the documentation for CCER
, CC1E
is bit 0.
So we need to change just those bits - we do it by getting the existing value, masking out the old bits with &
and ~
, and putting in new ones with |
like this:
// CC1E[0] = 0 (Turn channel 1 off)
poke16(CCER1, peek16(CCER1) & ~1);
// CC1S[1:0]=01 (rising edge), IC1F[7:4]=0 (no filter)
poke16(CCMR1, (peek16(CCMR1) & ~0b11110011) | (0b00000001));
And then...
- Select rising edge polarity by writing
CC1P=0
andCC1NP=0
in theCCER
register.
Looking at the reference again, CC1P
is bit 1, and CC1NP
is bit 3.
However in the last step we turned the channel off, so let's turn it back on as well.
// CC1P=0, CC1NP=0 (detect rising edge), CC1E[0] = 1 (Turn channel 1 on)
poke16(CCER, peek16(CCER) & ~(0b1011) | (0b0001));
Make sure the 3 multiplexers are forwarding the signal from A8 to the right place
The page also says:
Configure the timer in external clock mode 1 by writing
SMS=111
in theSMCR
register.Select
TI1
as the trigger input source by writingTS=101
in theSMCR
register (it actually says writeTS=110
forTI2
, butTI1
is what we want)
SMS
is bits 2:0
and TS
is 6:4
, so:
// SMS[2:0]=111 (ext clock), TS[6:4]=101 (CH1 as trigger)
poke16(SMCR, (peek16(SMCR) & ~0b1110111) | 0b1010111);
It also says:
- Enable the counter by writing
CEN=1
in theCR1
register
But Espruino already did that for us with analogWrite
.
Resetting registers
We just do this with:
// Prescaler to 0 - use every transition
poke16(PSC, 0);
// auto-reload with the full range of values
poke16(ARR, 65535);
However there's another footnote:
PSC contains the value to be loaded in the active prescaler register at each update event (including when the counter is cleared through UG bit of TIMx_EGR register or through trigger controller when configured in "reset mode").
So we've got to do that...
// poke the UG[0] bit to reset the counter and update the prescaler
poke16(EGR, 1);
And putting it all together we have:
// slave mode control register
var SMCR = 0x40010008;
// event generation register
var EGR = 0x40010014;
// Capture compare mode register
var CCMR1 = 0x40010018;
// Capture/compare enable register
var CCER = 0x40010020;
// counter
var CNT = 0x40010024;
// prescaler
var PSC = 0x40010028;
// auto reload register
var ARR = 0x4001002C;
// enable PWM on A8 (TIM1 CH1)
analogWrite(A8,0.5,{freq:10});
// CC1E = 0 (Turn channel 1 off)
poke16(CCER, peek16(CCER) & ~1);
// CC1S[1:0]=01 (rising edge), IC1F[7:4]=0 (no filter)
poke16(CCMR1, (peek16(CCMR1) & ~0b11110011) | (0b00000001));
// CC1P=0, CC1NP=0 (detect rising edge), CC1E[0] = 1 (Turn channel 1 on)
poke16(CCER, peek16(CCER) & ~(0b1011) | (0b0001));
// SMS[2:0]=111 (ext clock), TS[6:4]=101 (CH1 as trigger)
poke16(SMCR, (peek16(SMCR) & ~0b1110111) | 0b1010111);
// Prescaler to 0 - use every transition
poke16(PSC, 0);
// auto-reload with the full range of values
poke16(ARR, 65535);
// poke the UG[0] bit to reset the counter and update the prescaler
poke16(EGR, 1);
You can now look at the counter contents with peek16(CNT)
- it should return 0.
But now, if you turn A5
on and off (you connected it to A8
earlier) with digitalWrite(A5,1);digitalWrite(A5,0);
it should increase the counter.
Check the counter again with peek16(CNT)
- it should return 1.
Now if you do lots of pulses:
for (var i=0;i<1000;i++) {
digitalWrite(A5,1);digitalWrite(A5,0);
}
And then peek16(CNT)
, it should return 1001.
If you wanted to measure frequency, you could now use setInterval
to check the value of CNT
every second. The amount it increased would tell you the frequency of the square wave on A8
.
TIM1
itself is only 16 bit so this may not be as useful as you want. However other timers such as TIM2
and TIM5
behave in exactly the same way (you can just change the base address from 0x40010000
to the base address of the other timer), and have a 32 bit counter. The only other thing you'll have to do is to use peek32
instead of peek16
to read the counter.
Input Capture
Input capture is another useful function. In this mode, you can set CNT
to run at whatever speed you want (with analogWrite(A8, 0.5, {freq : my_frequency})
), but every time a bit changes state it'll save the value of CNT
into the relevant CCR
register.
For this we'll use the timer in this configuration:
The relevant section of the reference manual is 12.3.6 Input capture mode
, but I won't cover it in detail here.
All we need to do is:
- Enable and configure the counter (prescaler, autoreload) with
analogWrite
- Reconfigure Channel 1 to listen for events, rather that outputtting PWM
Obviously the first step is easy, and for the second step we can actually steal some of the code that we'd written previously for the counter - with one small tweak. This time we're using channel 1's prescaler IC1PS
, so we want to make sure we reset it's value as well so it doesn't do anything. It's just a matter of making sure we clear 2 extra bits in the CCMR1
register:
// Status Register
var SR= 0x40010010;
// Capture/compare enable register
var CCER = 0x40010020;
// Capture compare mode register
var CCMR1 = 0x40010018;
// counter
var CNT = 0x40010024;
// Capture Compare 1
var CCR1 = 0x40010034;
// enable PWM on A8 (TIM1 CH1)
analogWrite(A8,0.5,{freq:10});
// CC1E = 0 (Turn channel 1 off)
poke16(CCER, peek16(CCER) & ~1);
// CC1S[1:0]=01 (rising edge), IC3PSC[3:2]=00 (no prescaler), IC1F[7:4]=0 (no filter),
poke16(CCMR1, (peek16(CCMR1) & ~0b11111111) | (0b00000001));
// CC1P=0, CC1NP=0 (detect rising edge), CC1E[0] = 1 (Turn channel 1 on)
poke16(CCER, peek16(CCER) & ~(0b1011) | (0b0001));
And that's it. We can check that the counter is rising by looking at peek16(CNT)
- the number you get should keep changing.
However, if you check the Capture Compare Register for channel 1 with peek16(CCR1)
it shouldn't stay the same. You can also check whether it has triggered (register CC1IF
) using peek16(SR)&2
, and this should return 0
.
But now, assuming we've still got A8
connected to A5
from the last bit of code, we can raise and lower A8
and see what gets captured:
digitalWrite(A5,1);digitalWrite(A5,0);
Typing peek16(SR)&2
now will return nonzero, showing something was captured. And if we check the capture compare register with peek16(CCR1)
we'll see it has changed.
The act of reading CCR1
actually cleared the CC1IF
flag, so peek16(SR)&2
will now return 0.
But what if the timer triggers twice, before we can read the last value? We can detect that too - that's in the Capture Compare 1 Overflow flag
CC1OF
, which you can check with peek16(SR)&512
.
This may have marked an overflow already, and it can be cleared with poke16(SR,peek16(SR)&~512)
. But now, if you pulse the pin twice, without reading from CCR1
, the overflow flag will get set.
Capacitive Touch Sensor
Input capture really shines when you use it alongside another timer channel on the same timer. Let's say you use pin A10
on the Pico (TIM1_CH3
) as a normal PWM output, but then enable capture compare on A8
using the code above. You can now measure how long it takes A8
's input to rise after A10
's output rose.
It turns out this is very useful for capacitive touch (amongst other things).
Remove everything from the breadboard apart from the Pico, and then get a 1 Million Ohm resistor (100k Ohm will do, just not as well) and connect it between A10
(on the small holes at the end of the board - the resistor should just push into the hole) and A8
. Now get a 10cm length of wire, bend it into a circle, and connect it to A8
as well. What you've got now is a very large resistor, and a very small capacitor (the wire loop). When you move your hand near the capacitor your body increases the size of the capacitor.
So what does this mean? Well, as the capacitor gets bigger, it takes longer to charge and discharge (which is done via the resistor connected to A10
). Using Input Capture we can detect this (without having to use any computational time in JavaScript).
Simply upload the following code:
// Status Register
var SR= 0x40010010;
// Capture/compare enable register
var CCER = 0x40010020;
// Capture compare mode register
var CCMR1 = 0x40010018;
// counter
var CNT = 0x40010024;
// Capture Compare 1
var CCR1 = 0x40010034;
var PSC = 0x40010028;
// enable PWM on A8 (TIM1 CH1)
analogWrite(A8,0.5,{freq:1000});
// enable PWM on A10 (TIM1 CH3)
analogWrite(A10,0.5,{freq:1000});
// CC1E = 0 (Turn channel 1 off)
poke16(CCER, peek16(CCER) & ~1);
// CC1S[1:0]=01 (rising edge), IC3PSC[3:2]=00 (no prescaler), IC1F[7:4]=0 (no filter),
poke16(CCMR1, (peek16(CCMR1) & ~0b11111111) | (0b00000001));
// CC1P=0, CC1NP=0 (detect rising edge), CC1E[0] = 1 (Turn channel 1 on)
poke16(CCER, peek16(CCER) & ~(0b1011) | (0b0001));
function getCap() { return peek16(CCR1); }
This is identical to the Input Capture code, but:
- The frequency is now 1000Hz
- We're writing a square wave to A10 as well now
- We put the read of
CCR1
into a convenience function
So now, if you call getCap()
you should get a number (which depends on the resistor you used, and the capacitance of the coil of wire).
But, if you keep calling getCap()
while moving you hand near the wire, when you hand gets within less that a centimeter of the wire you should see the value rise up. If you were to call getCap()
from setInterval
like this:
// a value slightly above what you get from getCap() when you hand isn't close
var thresh = 300;
setInterval(function () {
digitalWrite(LED1, getCap() > thresh);
}, 10);
Then you'd have your own capacitive touch sensor!
This page is auto-generated from GitHub. If you see any mistakes or have suggestions, please let us know.